Premier Metal Fabrication Solutions for High-Quality Automotive Plastic Part Manufacturing
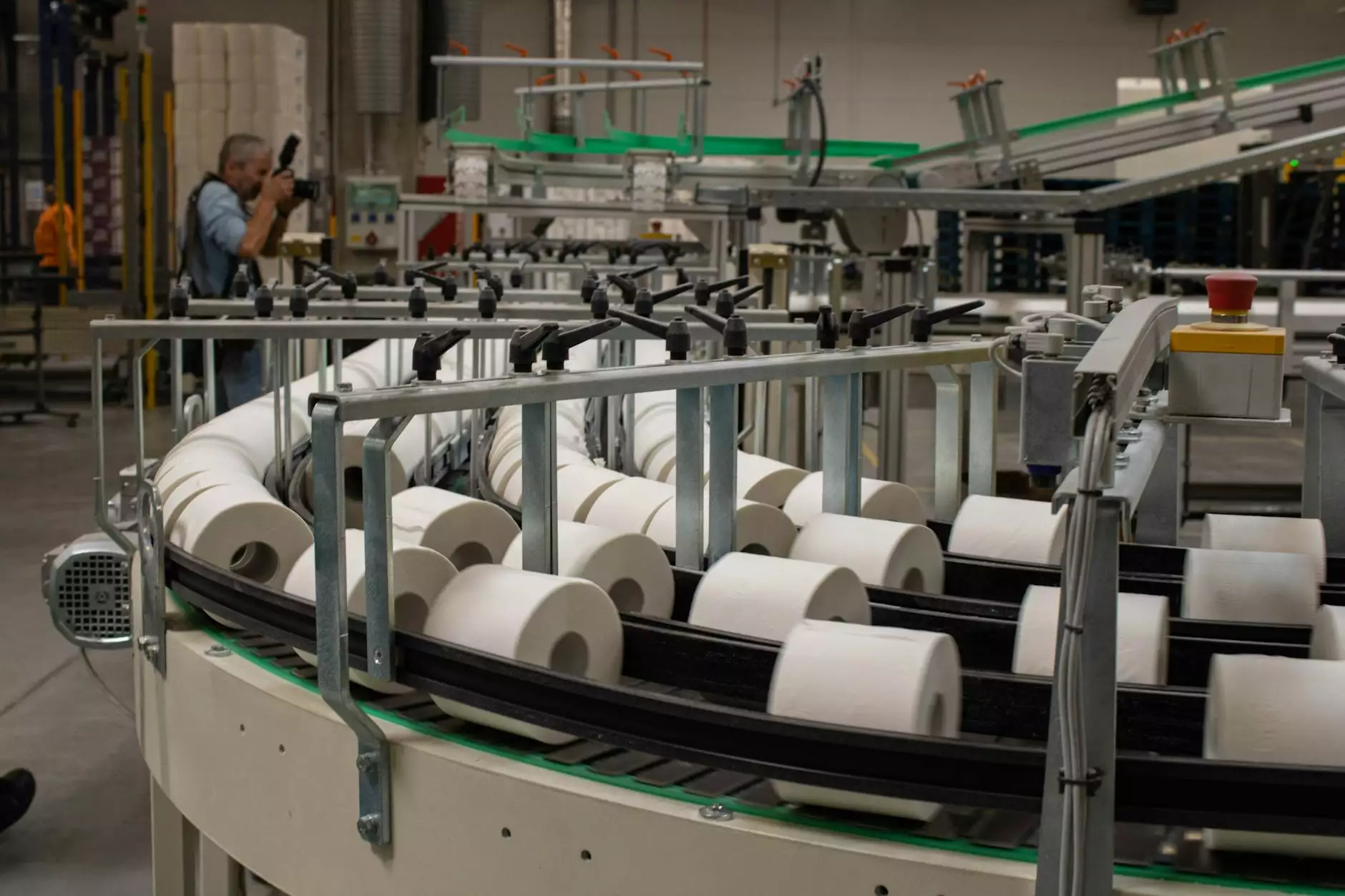
In the rapidly evolving automotive industry, precision, durability, and innovative manufacturing techniques are paramount. As manufacturers aim to produce lightweight, reliable, and cost-effective components, the role of advanced metal fabrication services becomes increasingly vital. Deep Mould, a leading name in Metal Fabricators, offers unmatched expertise and state-of-the-art technology to develop and produce automotive plastic parts that meet rigorous industry standards.
Understanding the Importance of Metal Fabrication in Automotive Plastic Part Production
At the core of creating high-quality automotive plastic parts is a synergistic relationship between plastics and metals. Metal fabrication plays a crucial role in mold making, structural supports, and assembly fixtures that facilitate the production of complex plastic components. The integration of precise metal components enhances the durability, precision, and functionality of the final automotive products.
The Symbiotic Relationship Between Metal Fabrication and Automotive Plastic Parts
- Precision Mold Manufacturing: Metal fabrication techniques such as CNC machining and laser cutting provide the exact molds necessary for injection molding processes.
- Structural Support and Reinforcement: Metal parts offer strength and stability to plastic components, especially in load-bearing automotive applications.
- Efficient Assembly: Custom metal fixtures streamline production and assembly lines, reducing cycle times and ensuring high-quality output.
Deep Mould's Expertise in Metal Fabrication for Automotive Plastic Components
Deep Mould boasts a comprehensive suite of metal fabrication capabilities tailored for manufacturing automotive plastic parts. Our facilities incorporate cutting-edge CNC machining, precision welding, laser cutting, and surface finishing technologies designed to meet, if not exceed, the stringent standards of the automotive industry.
Advanced CNC Machining for Precision Mold Components
Our CNC machining centers enable us to produce complex, high-precision metal molds essential for creating flawless automotive plastic parts. With meticulous attention to detail, we ensure every mold features tight tolerances, smooth finishes, and durable structures that withstand the demands of high-volume production.
Laser Cutting for Rapid prototyping and Customization
Laser cutting technology allows us to rapidly produce custom metal parts with intricate geometries. This flexibility facilitates rapid prototyping of automotive plastic parts, allowing manufacturers to test and refine their designs swiftly and cost-effectively.
Welding and Surface Finishing for Durability
Our expert welding services guarantee strong, reliable joints in metal components, while our surface finishing options—such as polishing, galvanizing, and coating—enhance corrosion resistance and aesthetic appeal. Such treatments extend the lifespan of metal fixtures and support structures in automotive environments.
Key Benefits of Choosing Deep Mould for Automotive Plastic Part Metal Fabrication
1. Unmatched Precision and Quality
Our manufacturing process emphasizes precision at every step, ensuring that the metal components used in creating automotive plastic parts align perfectly with industry specifications. This meticulous attention to detail results in components that fit seamlessly, function reliably, and meet safety standards.
2. Comprehensive Customization Options
Deep Mould offers fully customized metal fabrication services tailored to specific project requirements. Whether you need specific alloys, complex geometries, or special surface treatments, our team collaborates closely with clients to deliver solutions optimized for their unique needs.
3. Rapid Turnaround and Cost-Efficiency
Leveraging modern manufacturing technologies and experienced craftsmanship, we reduce lead times without compromising quality. Our efficient processes and scalable production capabilities help clients maintain competitive costs in the fast-paced automotive supply chain.
4. Compliance with Industry Standards
All our manufacturing practices adhere to automotive industry standards such as ISO 9001, IATF 16949, and TS16949. This commitment guarantees that all automotive plastic parts and related metal components meet rigorous safety, quality, and durability requirements.
Innovative Manufacturing Techniques Enhancing Automotive Plastic Parts Production
The integration of innovative technology in metal fabrication has revolutionized how automotive parts are designed, produced, and assembled. Deep Mould continuously invests in advanced machinery and methodologies to stay at the forefront of the industry.
1. Additive Manufacturing and Rapid Prototyping
Emerging additive manufacturing techniques enable us to produce complex, lightweight metal parts quickly. These prototypes significantly reduce development cycles for automotive plastic parts, allowing faster transitions from design to production.
2. Integration of Automation for Precision and Efficiency
Automation systems, including robotic welding and feeding mechanisms, improve the consistency and quality of metal components while reducing labor costs. Automated quality control processes ensure each piece conforms to tight tolerances and visual standards.
3. Surface Treatments for Extreme Conditions
Automotive applications often require parts with specialized coatings to withstand harsh environments. Deep Mould offers advanced surface treatments such as hard anodizing, powder coating, and anti-corrosion plating, which enhance the lifespan of metal fixtures in automotive contexts.
Why Metal Fabrication is Essential for High-Quality Automotive Plastic Parts
Manufacturers recognize that the synergy of high-quality metal components with automotive plastics results in durable, lightweight, and cost-effective products. Metal fabrication elevates the precision and structural integrity of plastic parts, ultimately contributing to better vehicle safety, performance, and aesthetics.
Enhanced Durability and Performance
Metal supports and inserts help resist wear and tear, mechanical stress, and temperature fluctuations, preserving the integrity of automotive plastic parts over extended periods. This durability is crucial for critical components like dashboards, bumpers, and interior trim.
Design Flexibility and Complexity
Complex geometries often require intricate molds and fixtures. Advanced metal fabrication techniques allow for the realization of highly detailed and customized plastic parts, tailored to specific automotive applications and aesthetic considerations.
Cost-Effective Mass Production
Precision metal molds and fixtures reduce waste, improve cycle times, and facilitate high-volume manufacturing. This efficiency translates into lower costs for automakers and suppliers, enabling competitive pricing for end consumers.
Partnering with Deep Mould: Your Trusted Metal Fabricator for Automotive Plastic Parts
Choosing the right partner is essential for achieving top-tier quality in automotive plastic part production. Deep Mould’s proven track record in metal fabrication positions us as a dependable, innovative, and customer-focused provider.
Our Commitment to Excellence
- Quality Assurance: Rigorous inspection protocols and adherence to international standards ensure each component meets quality benchmarks.
- Technical Expertise: Our team comprises highly skilled engineers and technicians experienced in automotive manufacturing requirements.
- Customer Collaboration: We work closely with clients from initial design through production to deliver tailored solutions and rapid prototyping.
- Sustainable Practices: We prioritize eco-friendly manufacturing processes, including waste reduction and environmentally safe surface treatments.
End-to-End Service for Seamless Production
From initial concept and mold design to final production, Deep Mould offers comprehensive support to streamline your development cycle. Our integrated approach minimizes delays, reduces costs, and guarantees the delivery of superior automotive plastic parts.
Future Trends in Metal Fabrication for Automotive Plastic Components
As the automotive industry shifts toward more sustainable, intelligent, and lightweight designs, the role of metal fabrication will become even more crucial. Some key trends include:
- Use of Advanced Alloys: Development of lighter yet stronger materials like aluminum, magnesium, and titanium alloys for improved support with reduced weight.
- Smart Manufacturing and IoT: Implementation of real-time monitoring and automation systems to optimize production efficiency and quality control.
- Sustainable Manufacturing: Focus on eco-friendly processes, recycling of metal scraps, and environmentally safe surface treatments.
- Hybrid Components: Integration of metal and plastic elements in complex automotive parts to optimize strength, weight, and cost.
Conclusion: Elevate Your Automotive Component Manufacturing with Deep Mould
In the competitive landscape of automotive manufacturing, exceptional quality, precision, and innovative solutions distinguish industry leaders. Deep Mould specializes in delivering top-tier metal fabrication services that bolster the production of automotive plastic parts. Our advanced technology, skilled team, and commitment to excellence ensure that your components meet the highest standards for durability, performance, and aesthetic appeal.
Partner with Deep Mould—your trusted metal fabricator—to transform your automotive parts manufacturing process and achieve unparalleled success in the industry. Contact us today to discover how our customized solutions can elevate your automotive products to new heights.