The Future of Manufacturing: Precision CNC Machining Parts Factories
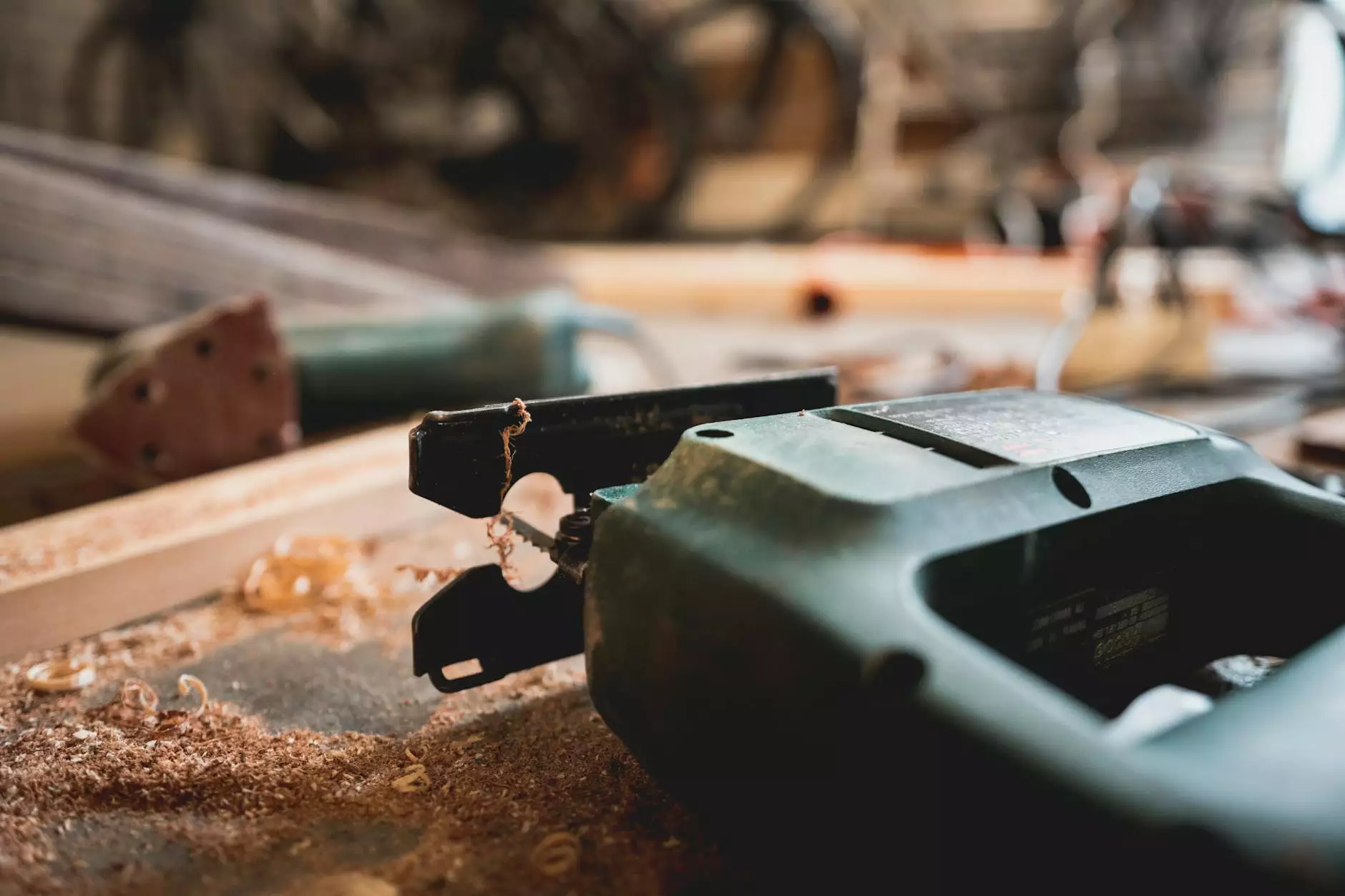
Precision CNC machining has emerged as a cornerstone technology in modern manufacturing, particularly within metal fabrication. In this detailed article, we will explore the intricacies of precision CNC machining parts factories, their significance, and the unmatched advantages they offer to various industries.
1. Understanding CNC Machining
CNC (Computer Numerical Control) machining refers to the automated control of machining tools via computer programming inputs. This method is vital for producing intricate components with high accuracy, and it has revolutionized the manufacturing landscape by:
- Enhancing Precision: CNC machines can produce parts with tolerances as tight as ±0.001 inches.
- Increasing Efficiency: Automated processes allow for faster production rates compared to manual machining.
- Reducing Waste: CNC machining optimizes material usage, minimizing scrap generation.
2. The Role of Precision CNC Machining Parts Factories
The factories that specialize in precision CNC machining parts are integral to a variety of sectors, including aerospace, automotive, medical, and electronics. These facilities utilize advanced machinery and sophisticated software to create components that meet the stringent demands of their clients.
2.1 Types of CNC Machining Processes
Precision CNC machining encompasses several techniques, each suited for different manufacturing needs:
- Milling: This process involves removing material from a workpiece using rotary cutters, allowing for complex shapes and features.
- Turning: A lathe machine rotates the workpiece, and a cutting tool shapes it, ideal for creating cylindrical parts.
- EDM (Electrical Discharge Machining): This technique uses electrical sparks to erode material, perfect for intricate designs.
- 3D Printing: An emerging technology in CNC machining, enabling rapid prototyping and production of complex geometries.
2.2 The Technology Behind CNC Machining
CNC machining relies on advanced technologies that include:
- CAD (Computer-Aided Design): Engineers design parts virtually using CAD software, allowing for precision and creativity.
- CAM (Computer-Aided Manufacturing): This software converts CAD designs into machine language, guiding CNC machines during production.
- Precision Tools: Incorporating specialized tooling for different machining operations ensures higher quality and durability of parts.
3. Benefits of Partnering with Precision CNC Machining Parts Factories
Companies that engage with precision CNC machining parts factories can reap significant benefits, including:
- Cost Efficiency: Reduced labor costs and optimized material usage translate to savings.
- High Quality and Consistency: Automated processes yield uniformity in production, ensuring quality control.
- Customization: Factories can easily adapt to specific client needs, offering tailored solutions for diverse applications.
- Scalability: Factories can ramp up production volumes quickly to meet market demands.
4. Selecting the Right Precision CNC Machining Parts Factory
Choosing the appropriate factory for your precision machining needs requires careful consideration. Here are key factors to evaluate:
4.1 Expertise and Experience
Look for factories with a proven track record in your industry. Experience matters, as it directly correlates with the quality of output and problem-solving capabilities.
4.2 Technology and Equipment
The capabilities of a factory depend greatly on its technology. Ensure that they utilize the latest CNC equipment and software, as these will influence the quality and efficiency of production.
4.3 Certifications
Choose factories that hold industry-standard certifications, such as ISO 9001, which indicate a commitment to quality management systems.
4.4 Communication and Support
Effective communication is critical in manufacturing. Opt for a factory that offers comprehensive support and is responsive to your inquiries.
5. The Future of Precision CNC Machining Parts Factories
The future landscape for precision CNC machining parts factories is poised for significant transformation. Here are emerging trends that are likely to shape the industry:
5.1 Automation and AI Integration
As factories look to increase efficiency, the integration of artificial intelligence and automation will become increasingly prevalent, optimizing operational workflows and enhancing predictive maintenance.
5.2 Sustainability Practices
With growing environmental concerns, factories are focusing on sustainable practices, including energy-efficient machines and eco-friendly materials, to minimize their carbon footprint.
5.3 Advanced Materials
The development of advanced materials, such as composites and alloys, will broaden the scope of applications in precision machining, enabling factories to produce stronger and lighter components.
5.4 Rapid Prototyping
The capability for rapid prototyping will enhance product development cycles, allowing for quicker iterations and faster time-to-market for innovative products.
6. Conclusion
In today’s manufacturing environment, precision CNC machining parts factories represent the pinnacle of productivity and quality. With their ability to deliver high-precision components, these factories are not just a choice but a necessity for industries aiming to stay competitive. As we look toward the future, embracing technological advancements and sustainable practices will be essential for these factories to continue thriving. By understanding their importance and potential, businesses can make informed partnerships that drive success and innovation.
For more information about industry-leading precision CNC machining services, visit deepmould.net today.