Unlocking the Power of Precision Injection Molded Plastics
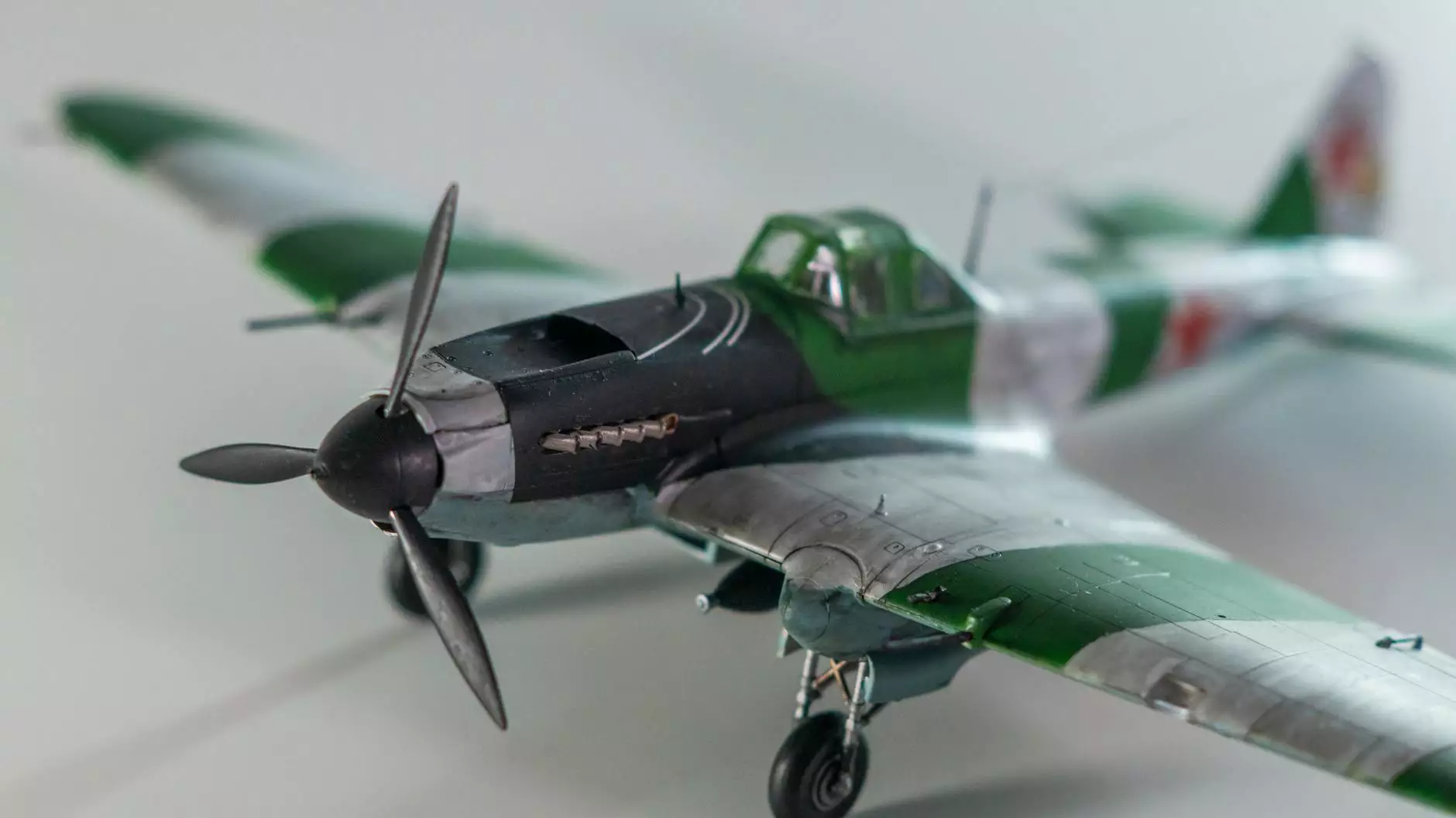
The manufacturing landscape has witnessed tremendous advancements over the past few decades, with precision injection molded plastics emerging as a pivotal force in various industries. From automotive components to medical devices, the ability to create high-quality, durable parts with exact specifications has transformed how manufacturers operate. At DeepMould.net, we are at the forefront of delivering exceptional metal fabricators that integrate seamlessly with the plastic molding process, ensuring precision in every product.
Understanding Precision Injection Molding
Precision injection molding is a manufacturing process that involves the creation of plastic parts by injecting molten plastic into a mold. This method allows for remarkable accuracy and repeatability, making it suitable for a wide range of applications. The technology behind this process has evolved, leading to innovative materials and techniques that enhance performance and efficiency.
The Process of Precision Injection Molding
The precision injection molding process involves several key stages:
- Material Selection: The quality of precision injection molded plastics largely depends on the material selected. Thermoplastics are commonly used due to their excellent properties like flexibility and impact resistance.
- Designing the Mold: A mold must be carefully designed to accommodate the specifications of the component, including tolerances, surface finish, and overall dimensions.
- Injection: The chosen plastic is heated until it becomes molten and is then injected into the mold under high pressure, allowing it to fill all cavities.
- Cooling: Once the mold is filled, the plastic is cooled to solidify, forming the final product.
- Removal: The solidified part is carefully removed from the mold, completing the manufacturing cycle.
Advantages of Precision Injection Molding
There are several significant benefits to using precision injection molded plastics in manufacturing:
- High Accuracy: Injection molding can achieve tolerances of +/- 0.001 inches, which is critical for components that must fit together perfectly.
- Cost-Effectiveness: Mass production using this method reduces costs significantly compared to many other manufacturing methods.
- Flexibility: A wide range of materials can be used, including various thermoplastics and composites, allowing manufacturers to choose based on their specific needs.
- Reduced Waste: The precision of the injection molding process minimizes material waste, aligning with the sustainable practices many companies are adopting today.
- Complex Designs: Injection molding can create intricate designs that may be challenging to produce using traditional manufacturing methods.
The Role of Metal Fabricators in the Process
In the world of plastic injection molding, metal fabricators play a critical role. They provide the molds that form the components, and their expertise in crafting high-quality molds directly influences the efficiency and effectiveness of the injection process.
Collaboration Between Metal Fabricators and Plastic Molding Companies
The synergy between metal fabricators and precision injection molding companies is vital for success. Each entity brings unique expertise to the table, ensuring that the final product meets stringent quality standards. At DeepMould.net, we prioritize this collaboration, understanding that the quality of the mold directly impacts production outcomes.
Industries Utilizing Precision Injection Molded Plastics
The versatility of precision injection molded plastics means they are utilized in a wide variety of industries:
1. Automotive Industry
The automotive sector heavily relies on precision injection molded components for various parts such as interior fittings, dashboard components, and under-the-hood elements. These parts must withstand high temperatures and stress while maintaining high precision.
2. Medical Sector
Medical devices, including syringes, connectors, and casings, often utilize precision injection molded plastics due to the stringent requirements for hygiene and exact specifications. The ability to produce sterile, accurate components is critical in this field.
3. Consumer Goods
From kitchenware to toys, consumer products benefit from the durability and design flexibility afforded by injection molding. This not only enhances the aesthetic appeal but also ensures functionality.
4. Electronics
Components such as casings for smartphones and other devices require precision and minimal tolerances to ensure fitment and protection. Injection molding provides these attributes efficiently.
Choosing the Right Partner for Precision Injection Molded Plastics
When selecting a partner for precision injection molded plastics projects, several factors should be considered:
- Experience: Choose a company with proven experience in the specific application area.
- Technological Capability: Ensure they utilize advanced machinery and technology for mold design and production.
- Quality Assurance: A strong emphasis on quality control and industry certifications is essential.
- Customization: The ability to customize molds and processes to meet specific product requirements can significantly affect the project's outcome.
- Customer Support: A responsive team capable of providing ongoing support and guidance throughout the process is invaluable.
Future Trends in Precision Injection Molded Plastics
The future of precision injection molded plastics shows great promise, with several trends poised to shape the industry:
1. Sustainable Practices
As environmental concerns rise, the demand for biodegradable materials and sustainable manufacturing processes is growing. Innovations in materials science are leading to the development of eco-friendly thermoplastics that can be used without compromising quality.
2. Advanced Automation
The integration of automation and robotics into the injection molding process enhances speed, precision, and efficiency, reducing the likelihood of errors and downtime.
3. Smart Manufacturing
The incorporation of Internet of Things (IoT) technology provides real-time data on production processes, enabling manufacturers to optimize operations and reduce costs.
4. Shortened Product Development Cycles
With advancements in rapid prototyping and 3D printing, the time taken to design and produce new products is decreasing, allowing companies to respond faster to market demands.
Conclusion
The world of precision injection molded plastics is vast and continuously evolving, offering exciting opportunities for businesses across various sectors. As a company specializing in metal fabricators, DeepMould.net stands ready to deliver innovative solutions that meet the rigorous demands of the industry. By harnessing the power of precision molding, businesses can achieve unparalleled quality and efficiency in their manufacturing processes, ensuring they remain competitive in an ever-changing market.
Investing in precision injection molding is not just a manufacturing choice; it’s a step towards embracing a future defined by quality, durability, and sustainability.