The Essential Role of PLC Maintenance in Industrial Automation
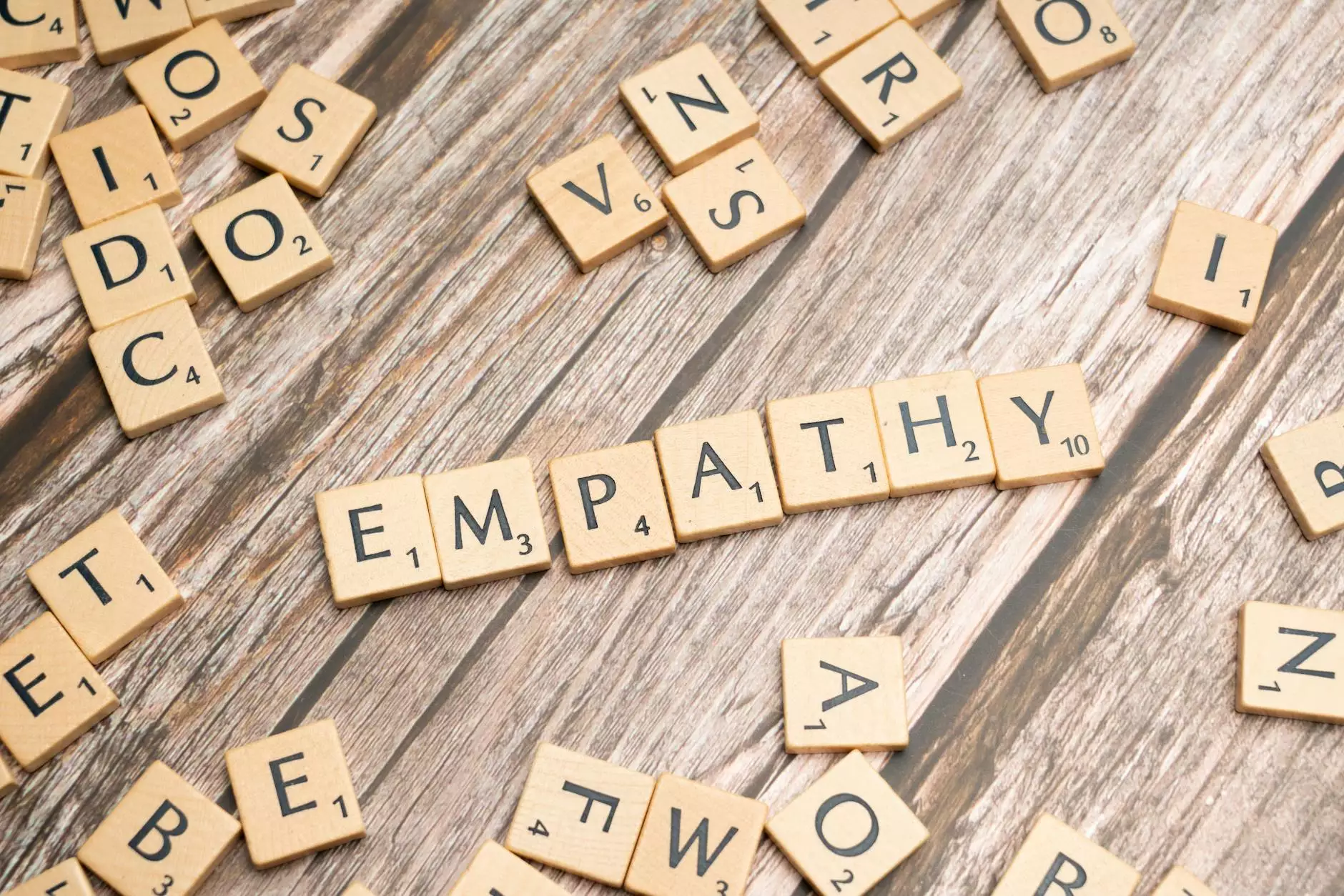
In today's rapidly evolving industrial landscape, the importance of maintaining efficient and reliable automation systems cannot be underestimated. As automation technologies continue to advance, organizations are increasingly relying on programmable logic controllers (PLCs) to streamline operations, enhance productivity, and minimize downtime. This article will delve into the critical aspects of PLC maintenance and the vital role played by a PLC maintenance technician in ensuring seamless operations.
Understanding PLCs: The Backbone of Modern Automation
A Programmable Logic Controller (PLC) is a ruggedized computer used for industrial automation. It is designed to control machinery and processes, enabling manufacturers to automate repetitive tasks effectively. PLCs operate through your organization's unique program, handling inputs from various sensors and making decisions based on predefined parameters.
Key Components of a PLC
- Input/Output Modules: Interfaces between the PLC and field devices.
- Central Processing Unit (CPU): The brain of the PLC that processes the control instructions.
- Power Supply: Powers the PLC and its components.
- Programming Device: Allows engineers to program the PLC, typically using ladder logic or other programming languages.
The Critical Importance of PLC Maintenance
Just like any other technology, the effectiveness of a PLC diminishes over time if not properly maintained. Efficient PLC maintenance is essential for ensuring that the automation systems operate at optimal performance levels. Neglecting maintenance can lead to serious issues, including:
- Unexpected Downtime: Unplanned outages can severely impact production and lead to significant financial losses.
- Decreased Efficiency: Inefficient systems consume more energy and resources, increasing operational costs.
- Compromised Safety: Faulty PLCs can lead to unsafe conditions, posing risks to employees and equipment.
- Reduced Equipment Lifespan: Regular maintenance can prolong the life of PLC systems and connected machinery.
Who is a PLC Maintenance Technician?
A PLC maintenance technician is a skilled professional responsible for the upkeep, troubleshooting, and repair of PLC systems. This role is critical in industries where automation is a significant part of the production process, such as manufacturing, energy, and water treatment.
Primary Responsibilities of a PLC Maintenance Technician
The responsibilities of a PLC maintenance technician encompass various tasks, including but not limited to:
- Monitoring Systems: Regularly checking the operation of PLCs and associated equipment.
- Troubleshooting: Identifying and resolving issues that arise in the PLC systems.
- Programming Adjustments: Modifying existing programs to improve system performance.
- Routine Inspections: Performing planned maintenance to prevent system failures.
- Documentation: Keeping detailed records of maintenance activities and system changes.
Essential Skills of a PLC Maintenance Technician
A successful PLC maintenance technician should possess a range of technical and personal skills, including:
- Technical Expertise: Strong understanding of PLC hardware and software.
- Problem-Solving Abilities: Ability to diagnose and resolve technical issues effectively.
- Attention to Detail: Precision in programming and maintenance tasks is essential to avoid future problems.
- Communication Skills: Ability to communicate effectively with team members and stakeholders.
- Continuous Learning: Keeping up-to-date with the latest PLC technologies and maintenance techniques.
Best Practices for Effective PLC Maintenance
To ensure peak performance and longevity of PLC systems, adhering to best practices for maintenance is crucial. Here are some strategies that businesses can implement:
1. Scheduled Maintenance
Establish a robust schedule for routine maintenance checks. This can include checking connections, inspecting hardware for wear and tear, and reviewing program logic for efficiency. By addressing potential problems proactively, organizations can prevent costly downtime.
2. Regular Software Updates
Keeping the PLC software updated ensures that the system operates with the latest features and security enhancements. Outdated software can lead to vulnerabilities that may compromise system integrity.
3. Training and Development
Continuous training for PLC maintenance technicians is vital. Offering educational opportunities on new technologies, troubleshooting techniques, and best practices ensures that your team remains competent and competitive.
4. Documentation and Records
Maintain detailed records of maintenance activities, system changes, and any issues encountered during operation. Having this information readily available can expedite troubleshooting and inform future maintenance strategies.
5. Collaborate with Distributors
Partnering with experienced electronic component distributors, such as QF Automation, can provide access to high-quality components and expert advice, enhancing overall maintenance procedures.
The Role of Electronic Components Distribution in Maintenance and Automation
As a leading electronic components distributor in Canada, QF Automation plays a pivotal role in the efficiency of PLC maintenance and operations. Access to quality components and timely support minimizes delays in repair and system upgrades.
Benefits of Collaborating with a Distributor
- Quality Assurance: Distributors vet their suppliers, ensuring that only top-tier components are supplied.
- Market Reach: Distributors like QF Automation provide a wide array of components that meet various industrial requirements.
- Expert Consultation: They often have knowledgeable personnel who can offer guidance on component selection, best practices, and integration.
- Streamlined Procurement: Efficient supply chains make acquiring necessary components quicker and more affordable.
Future Trends in PLC Maintenance and Automation
The landscape of industrial automation is continually changing, and various trends are shaping the future of PLC maintenance, including:
1. Predictive Maintenance
By utilizing advanced analytics and IoT technologies, predictive maintenance allows technicians to foresee potential failures and schedule interventions before problems escalate.
2. Remote Monitoring
With the rise of Industry 4.0, remote monitoring solutions enable real-time oversight of PLC systems, reducing the need for on-site visits and facilitating timely responses to issues.
3. Increased Integration with AI
Artificial intelligence is beginning to play a role in optimizing PLC functions and maintenance strategies. AI can analyze vast amounts of data to recommend maintenance schedules and predict equipment failures.
Conclusion
In conclusion, the role of a PLC maintenance technician is fundamental to the operational success of modern automation systems. By investing in effective maintenance practices, organizations not only enhance productivity but also ensure safety and efficiency in industrial processes. Collaborating with reputable electronic components distributors like QF Automation equips businesses with the necessary tools and support to thrive in today's competitive environment. Embracing innovative maintenance strategies will further bolster an organization's capabilities, preparing them for the future of automation.
For comprehensive solutions in electronic components distribution and PLC repair services, QF Automation stands as a reliable partner, committed to supporting your business's automation needs.